We have the right solution for your needs
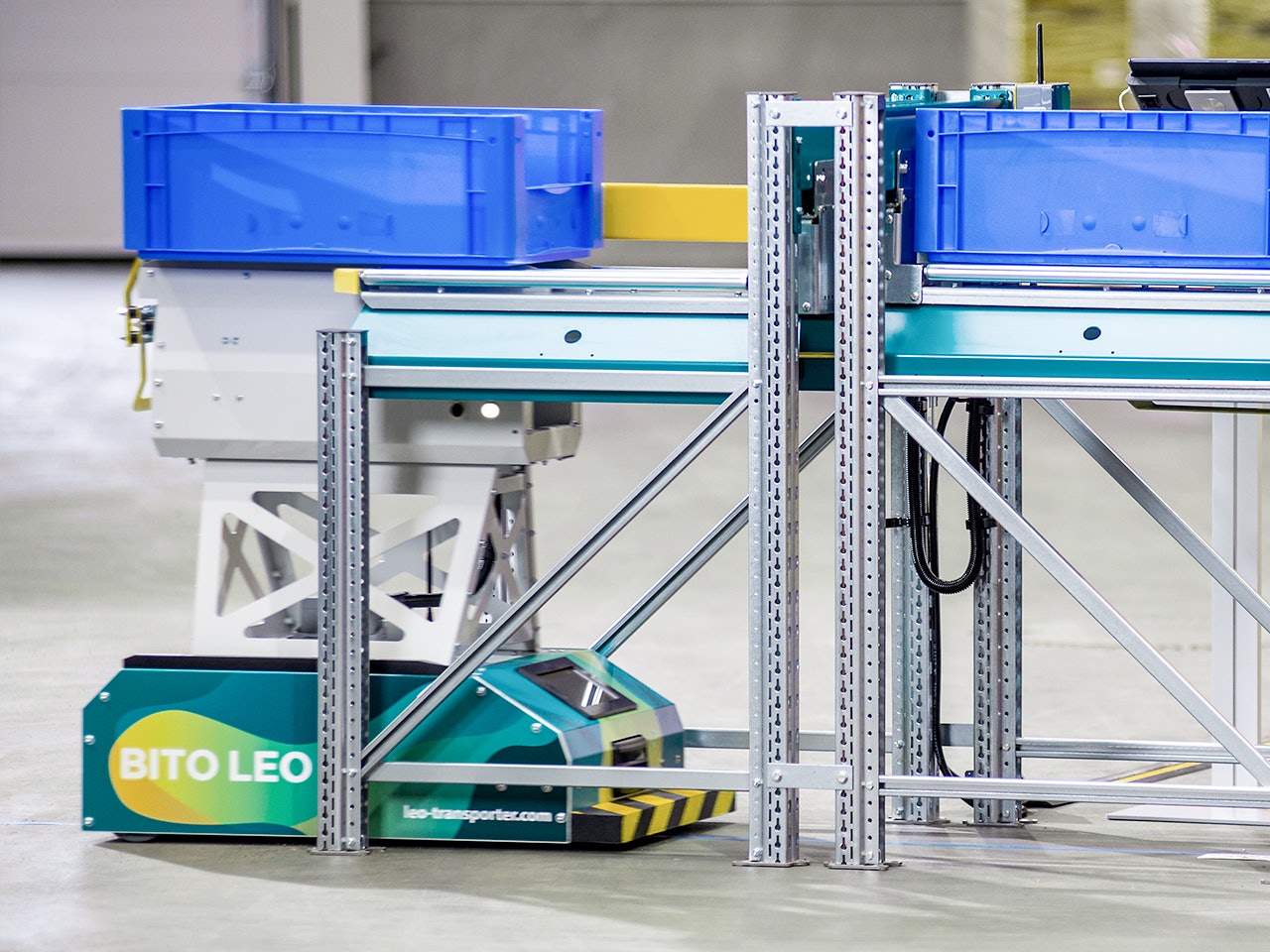
The BITO LEO transporters have already convinced a large number of customers with numerous solutions in various application areas in logistics and e-commerce. In order to always meet the needs of our customers and the dynamic market conditions, we are constantly developing our products further to expand our product family. To be able to offer a solution for diverse applications, our product range consists of three BITO LEO transporters.
Whether LEO locative, custom, flow or carrier - the various BITO transporters fulfil almost every requirement in terms of material flow automation
- LEO locative ideal for trays, containers and cardboard boxes
- LEO custom ideal for customers who require customised solutions for their processes
- LEO flow ideal for all applications with solid containers in combination with conveyor technology
- LEO carrier ideal for order picking, distribution of goods and much more
Book an appointment!
Use our online booking calendar to arrange an appointment with our BITO LEO experts.
Applications in various areas of logistics/e-commerce
Incoming goods for storage
Challenge:
A logistics service provider receives its goods on pallets. The goods are separated from the pallets into containers or cartons and then transported to the various warehouses for collection. The goods are separated in batches and faster than they are collected. For this reason, a buffer warehouse is required for decoupling. Empty containers are produced during collection and must be returned for separation.
LEO solution:
Employees separate the delivered goods into containers and place them on gravity roller conveyors. The last element of the roller conveyor is designed as a conveyor system and conveys the containers onto a LEO flow transporter. This is equipped with a scissor lift. The employees remove the empty containers from the roller conveyor [D] LEO flow takes the goods to the collection stations [B]. The collection points are equipped with a LEO buffer store. Each storage channel has 3 levels and can store a total of 24 containers or one Euro pallet. The buffer store thus decouples the incoming goods process and the collection process from each other in terms of time. Empty containers are placed on a roller conveyor [C] and returned to [D]. As an option, employees can prioritise storage during the separation process by selecting individual target channels.
Automatic loading of staging storage systems
The challenge:
The BITO piece goods flow system is used in a staging warehouse. The system enables high pick rates by minimising the walking distances and access times for the picker. The individual channels must be replenished regularly. For this purpose, buffer goods are stored in a small parts warehouse, for example a BITO multi-storey system. The replenishment containers should be refilled automatically to reduce labour requirements. Empty containers must also be brought to the small parts warehouse.
LEO solution:
A LEO flow with automatic lift is used. LEO flow transports empty containers from a return channel to the small parts warehouse. This signals which channel is required. LEO flow accepts a previously picked order and moves it directly to the target channel. The lift is activated and LEO releases the bin and travels to the return channel.
Picking for consolidation
Challenge:
The shipping orders are picked in different warehouses: simple shelves, floor levels in pallet racking, multi-level systems for B & C articles. Pick zones with piece goods flow system or lean lifts for A articles. The goods must be brought together and consolidated from these different warehouses. The consolidation process must be organised as efficiently as possible. Empty containers must be returned to the warehouses after consolidation.
LEO solution:
A shipping order consists of several items. These items can be stored in different warehouses and storage systems. A-items are stored directly from the pallet in pallet racking [A]. B-items are stored in a shelving rack [B] and C-items in a multi-level system. Each dispatch area is picked into one container per storage area. LEO flow collects these totes from a conveyor station and takes them to the consolidation area [D]. The area is equipped with six roller conveyors. By assigning the orders to different roller conveyors, the consolidation of the orders is ensured. A further conveyor technology element [E] enables empty containers to be returned to the picking areas.
Automatic loading of staging storage areas
Challenge:
The BITO piece goods flow system is used in a staging warehouse. The system enables high pick rates by minimising walking distances and access times for the picker. The individual channels must be replenished regularly. For this purpose, buffer goods are stored in a small parts warehouse, for example a BITO multi-storey system. The replenishment containers should be refilled automatically to reduce labour requirements. Empty containers must also be brought to the small parts warehouse.
LEO solution:
A LEO flow with automatic lift is used. LEO flow transports empty containers from a return channel to the small parts warehouse. This signals which channel is required. LEO flow accepts a previously picked order and moves it directly to the target channel. The lift is activated and LEO releases the container and travels to the return channel.