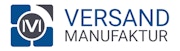
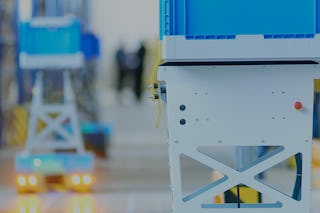
Versandmanufaktur
LEO locative for optimising material flow
About Versandmanufaktur
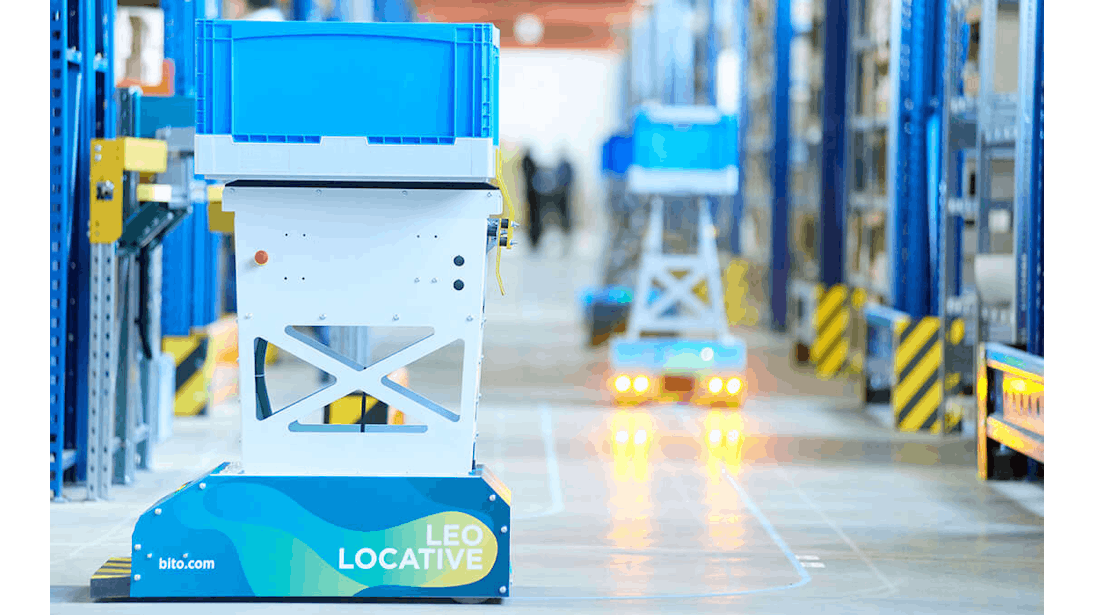
In 2009, under the name Trendcom GmbH, Frank Hammermeister opened his own logistics centre, switching from pure intralogistics consulting to fulfilment for e-commerce companies after many years. In 2017, the company was renamed Versandmanufaktur GmbH. Versandmanufaktur offers picking, packing, storage and shipping, returns management, quality management, packaging concepts, web shop and content maintenance, and order management. In 2016, the company moved into a former railway repair shop on the DB site in Witten, which covers around 5,500 square metres, and took over the existing warehouse technology. It now employs 120 people there.
Background and requirements
- The mail-order company stores, packages and ships over 70,000 products for its e-commerce customers in the fashion, food, interior/home design and cosmetics sectors on a 5,500 square metre site.
- Depending on the season, between 2,000 and 6,000 orders have to be processed each day. The service provider ships finished products to the end customers, packages orders and also assembles products individually.
- 50 % to 60 % expansion annually, in addition, 50 % of sales are achieved in the 4th quarter alone.
- The e-commerce business is subject to strong fluctuations, is growing strongly overall and is difficult to plan.
- The company was looking for a solution that would reduce the workload, enable a quick response and save valuable time.
- Therefore, automation in the area of warehouse technology is not possible. In order to reduce error rates and further optimise processes, the material flow is to be automated. In the past, the products were placed individually in a KLT container subdivided with hanging files and moved by employees on trolleys.
Efficiency increase at a glance
The BITO Solution
AGV with stations
» The system of LEO locative transporters and LEO locative stations works without Wi-Fi or IT and is controlled by an optical trail stuck to the ground and markers also placed on the ground.
Plug and Play
» It can be installed completely independently and used immediately. The optical tracking can be quickly adapted to new requirements.
decentralised target control
» The goods are sent from the starting point to any destination selected on a tablet using the LEO locative. The tablet sends the destination information via Bluetooth to a smart box attached to the LEO station that serves as the container transfer station (destination).
Customer application and the characteristics of the storage facility
- The five LEO locative transporters take on the long journeys to pick up the goods at the six LEO stations in front of the shelves and transport them to the assembly and dispatch stations.
- Currently, six destinations can be controlled via tablet. Stops and thus destinations are defined by corresponding markers on the floor.
- At the moment, LEO locative is used at Versandmanufaktur for 80% of its shipping and 20% of its goods storage. The latter area of application is to be expanded.
- Particularly in the area of product assembly and finishing, the complexity is very high. LEO transporters and stations equalise the structures in the material flow there.
Customer benefits
The BITO solution has provided the following benefits:
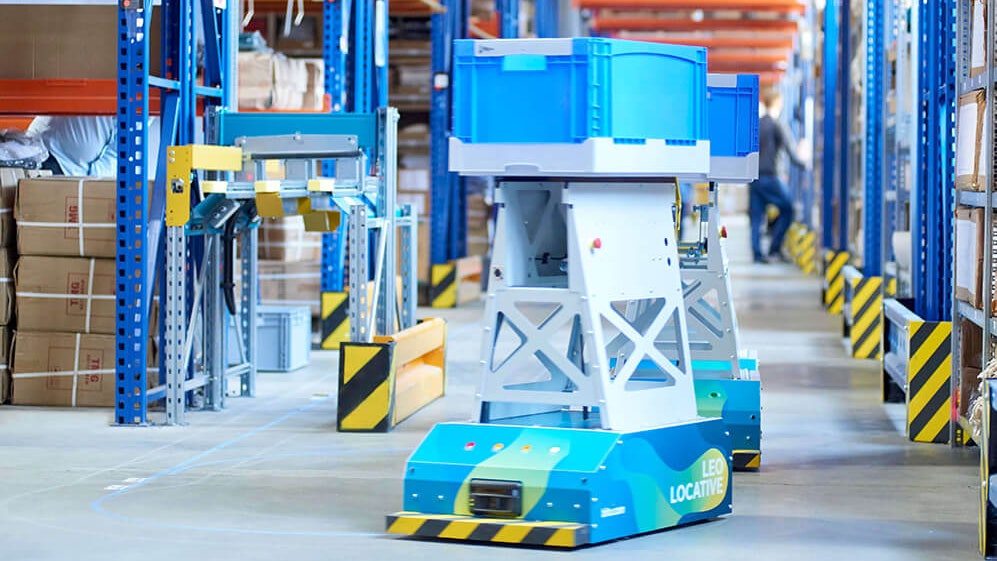
- Reducing the distances travelled by employees, thereby increasing the ergonomics of the workplaces.
- Automation of the material flow
- The system is flexibly adaptable and scalable.
- Straightening out the structures in the material flow. This helps to maintain high standards in the inhomogeneous environment of e-commerce.
- Only a tablet and not an expensive material flow computer is required for target control.
‘As a service partner in the field of fulfilment for online retail, we continue to operate in a very dynamic market with high growth rates, in which we also have an above-average share. It is important for our customers that we can react very flexibly with their products. True to our motto ‘Better building tents than castles’, we cannot and do not want to automate in the field of warehouse technology, but we do in the area of material flow. In this respect, the LEO locative system has convinced us because it offers the necessary flexibility and scalability that is important for us and our customers. A simple plug-and-play application in the truest sense of the word, which saves us many kilometres of mileage and, with a payback period of well under half a year, allows us to achieve a high level of cost-effectiveness.’
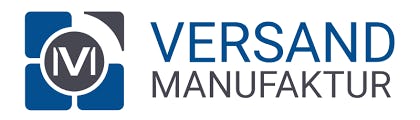